- Straightening Machines: Types, Functions, and Applications
- Essential Maintenance and Refueling Guide for Centerless Grinders
- Steel Peeling Machines: Advantages and Applications
- Why Choose Mingcheng Peeling Machine? Boost Production Efficiency and Create Dual Profits
- Metal Materials and Their Development Trends
- Lathes vs Milling Machines: Turning vs Milling
E-mail:liu@mingchenggroup.com
Phone:+86 13322202758
QQ:605712576
Address:No. 20, Gangwan Street, Zhongshan District, Dalian City, Liaoning Province
Optimizing Straightening Machines: Efficiency & Solutions
Understanding the straightening machine is crucial for optimizing metal processing. This equipment adjusts material straightness, which is key for ensuring product quality and production efficiency.
The choice between manual and automatic feeding methods impacts overall performance, with automatic systems offering greater productivity and safety. Regular maintenance and proper spindle speed adjustments are essential for achieving optimal processing results and extending equipment life. Investing in these technologies and practices enhances manufacturing efficiency and quality.
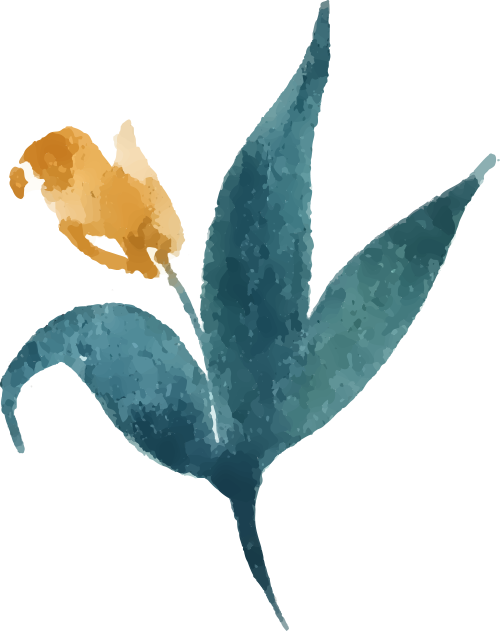
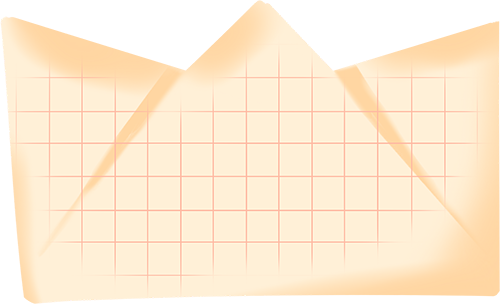
Feeding Method of Its Impact on Efficiency
Feeding Method of Its Impact on Efficiency
As an important piece of metal processing equipment, the straightening machine adjusts the material’s straightness and ensures production line quality. One key operating parameter is the feeding method, which affects processing efficiency and material handling safety.
There are two primary feeding methods for the straightening machine: manual and automatic. Manual feeding requires the operator to insert material section by section. This method demands high operator skill and is less efficient but is ideal for small batches or special material processing due to its flexibility. In contrast, the automatic feeding method uses a hydraulic or mechanical drive system for continuous material feeding. This approach significantly boosts production efficiency and reduces labor intensity. Automatic systems, equipped with sensors and controls, ensure proper material positioning and continuous supply, making them suitable for mass production and uniform material types.
When selecting a feeding method, consider production scale, material type, and budget. While automatic feeding involves a higher initial investment, its long-term efficiency benefits and lower labor costs offer a high return on investment. Moreover, it enhances work safety by reducing operator contact with the equipment. Maintaining the straightening machine is crucial, whether using manual or automatic feeding. Regular inspection, cleaning, and lubrication of the feeding mechanism are essential for smooth operation. Automatic systems, with their multiple precision parts, require more detailed and frequent maintenance.
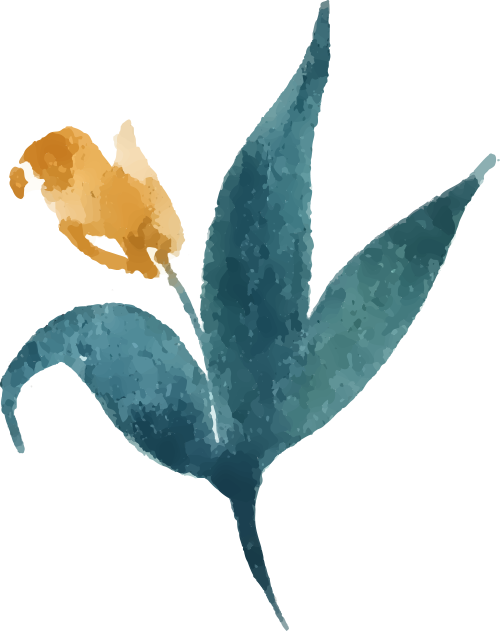
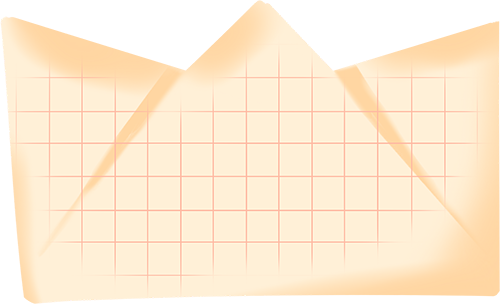
Influence of the Spindle Speed
Influence of the Spindle Speed
The spindle speed of the vertical straightener is a key parameter influencing production efficiency and processing quality. Spindle speed, measured in revolutions per minute (RPM), affects the workpiece's rotation speed during processing, impacting cutting force, heat distribution, and surface treatment.
Different materials and processing needs require varying spindle speeds. Higher speeds can enhance processing efficiency but may also lead to faster tool wear and reduced workpiece surface quality. Thus, selecting an appropriate spindle speed is crucial for maintaining quality. The spindle speed is also linked to other equipment parameters such as feed speed and cooling systems. Adjusting these parameters according to material characteristics and processing requirements is essential for optimal results. Overall, the spindle speed of the vertical straightening machine is critical for performance. Properly selecting and adjusting spindle speed can significantly improve production efficiency, ensure processing quality, and extend equipment lifespan.
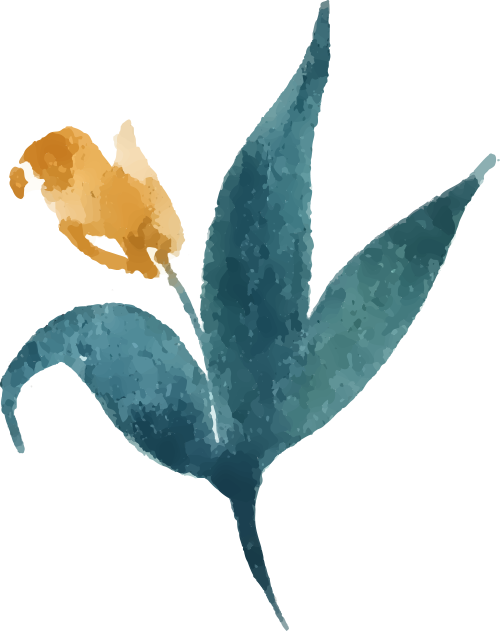
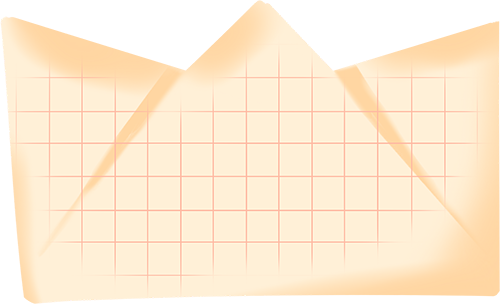
How to Avoid Factors That Lead to a Decline in the Efficiency
How to Avoid Factors That Lead to a Decline in the Efficiency
To avoid factors that lead to a decline in the efficiency of the straightening machine, first, address impurities. In harsh environments, use high-quality, compatible parts and lubricants to prevent harmful impurities. Additionally, ensure good mechanical protection at the work site to keep impurities out of the machine.
Temperature management is also crucial. Avoid operating the machine at low temperatures without proper preheating. Ensure the machine reaches the specified temperature before use. Also, prevent high-temperature operation by regularly checking the temperature gauge and stopping the machine for inspection if issues arise. Address faults promptly and check the cooling system regularly.
Finally, to prevent corrosion, take measures to minimize chemical corrosion based on local weather and air pollution. Protect the machine from rainwater and airborne chemicals.
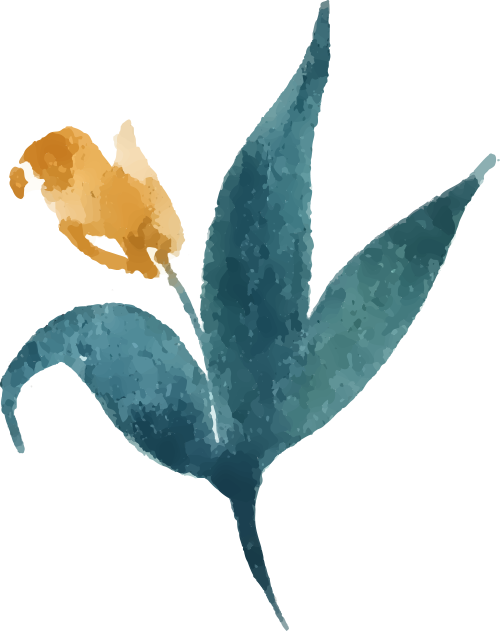
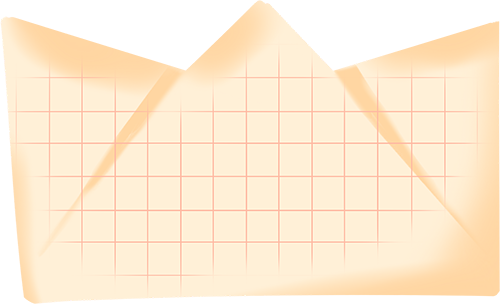
Welcome to Order from Us
Welcome to Order from Us
We invite you to place an order with us and experience our exceptional service. We offer customized solutions tailored to meet your specific needs and requirements. Our commitment to quality is backed by a comprehensive one-year warranty, ensuring peace of mind with your purchase.
With over ten years of experience in working with industrial furnaces, we have a deep understanding of the intricacies and demands of the industry. Our expertise enables us to provide not only top-notch products but also reliable support and maintenance services. Whether you need a solution for a unique application or ongoing support for your existing systems, we are here to help.
Contact us today to discuss your needs and discover how our advanced equipment and dedicated service can benefit your operations. We look forward to working with you and contributing to the success of your projects!
- Previous:Precision and Efficiency: Steel Tube Straightening Machines
- Next:The Past and Present of Centerless Grinders
-
2023-09-19How The Round Steel Peeling Machine Works?
-
2023-09-19Round Steel Peeling Machine